列车高速行驶时,车轮与铁轨摩擦,会产生很大的磨损。于是,如何制造安全耐用、性能还好的车轮,很长时间以来,都是困扰我国高铁发展的难题。
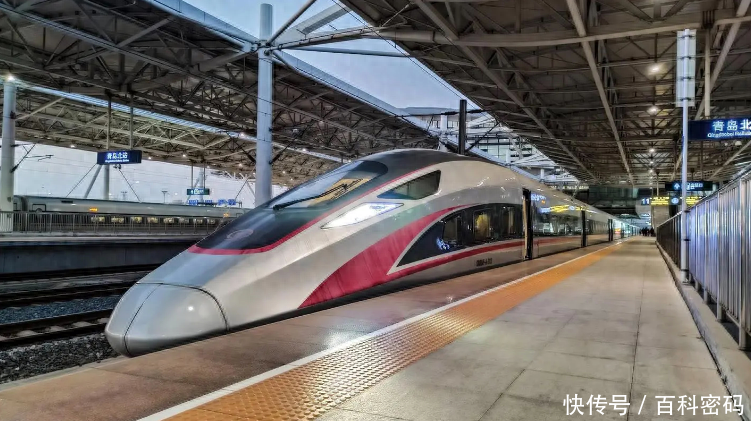
为何我国面临车轮技术垄断?
截止2023年底,我国铁路营业里程已经达到15.9万公里。其中,高铁线路总长度为4.5万公里,位居世界第一——而这,则意味着广阔的高铁车轮市场。
因为我国工业起步较晚,且高铁车轮生产技术复杂,在过去,我国需要面临来自日、德、法、意四国的技术垄断。
我国高铁早期发展时期,不得不向他们进口车轮,受制于工业的技术壁垒,处境十分被动。这些国家在获利的同时,还有意打压我国铁路发展,当中国向他们下达了价值5.6亿元人民币的订单后,他们竟然撕毁订单,使车轮断供的高铁系统面临巨大困境。
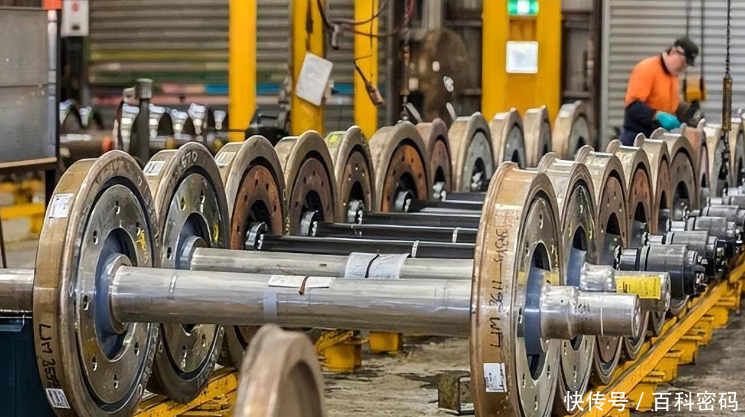
高铁车轮是世界上公认的技术要求高、生产难度大的尖端技术产品。为了维持自己的技术优势,这些国家坚持“三不原则”,即“不申报专利、不发表论文、不接受交流”,让其他国家无法引进生产车轮的先进技术。
之所以高铁车轮生产如此困难,是因为在高速条件下,车轮的受力状态较之常规使用条件发生了很大变化,为保证列车的安全运行,车轮必须具有更高的性能。仅仅是钢材中碳元素比例的变化,就很有可能导致裂纹的产生。
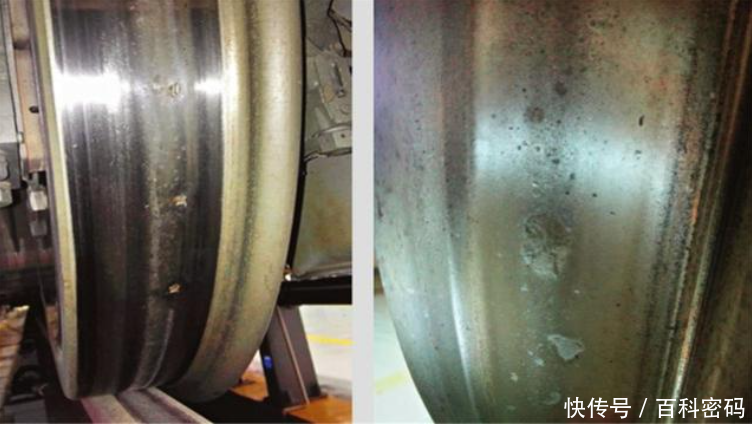
高铁车轮制造,为什么难?
那么,高铁车轮生产的技术难点究竟是什么?
这要从高铁车轮的制造过程说起。
从流程上,高铁车轮的生产过程大致可以分为钢坯冶炼、热成型、热处理三个工序,制作出成品后,再进行超声波检测、硬度测量、全尺寸测量等全方位严格检测,检测结果合格后,才能出厂。
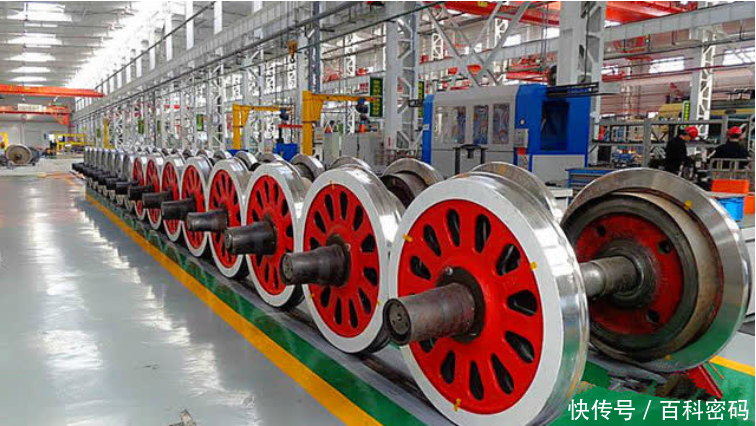
其中,钢坯冶炼是车轮生产的第一步。高铁车轮对钢材各方面的性能有较高要求,通常需要使用优质碳素钢和低合金钢等特殊钢型,从而需要对其中杂质的含量、化学成分的比例和分布有极为精准的把控。
若其中杂质含量高,会影响车轮的强度,当遇到异物磕碰时,更容易在表面形成疲劳裂纹,导致安全隐患。诸如在各种原材料的配比、炼铁时的温度控制、连铸过程中钢水是否会接触空气,冶炼过程中任何细微之处的调整,都会导致成品性能的变化。
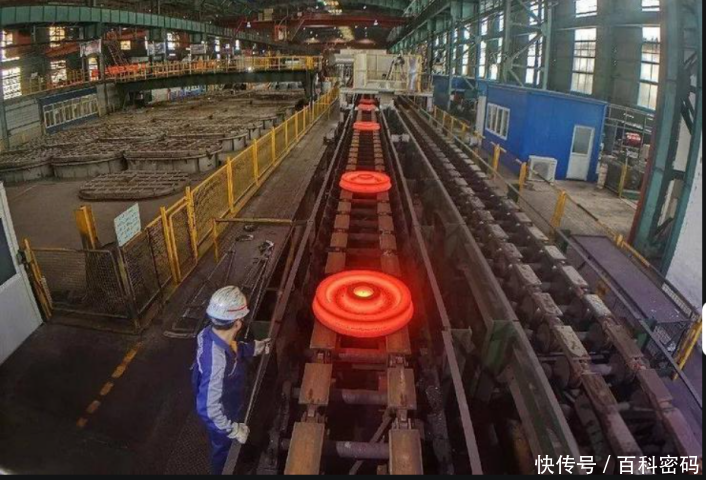
当液态的钢水变成固态的铸坯后,就进入了下一个步骤。热成型是将钢材加热到一定温度,施以变形力进行塑性形变,从而制造出各种构件,一般分为轧制、模锻两种工艺。之所以要加热钢材,是因为高温能提升钢材的可塑性和韧性,更便于车轮的塑形,但温度的改变也会使钢材发生化学和物理性质的变化。
不但加热到什么温度是一个重要问题,如果加热温度不均匀,还会导致其在成型过程中,出现变形不均、开裂、起皱等缺陷,使产品精度下降。因此,采用温度传感器等设备,对各部分温度进行实时监测,并随时调整加热参数,便成了把控车轮品质的重点之一。
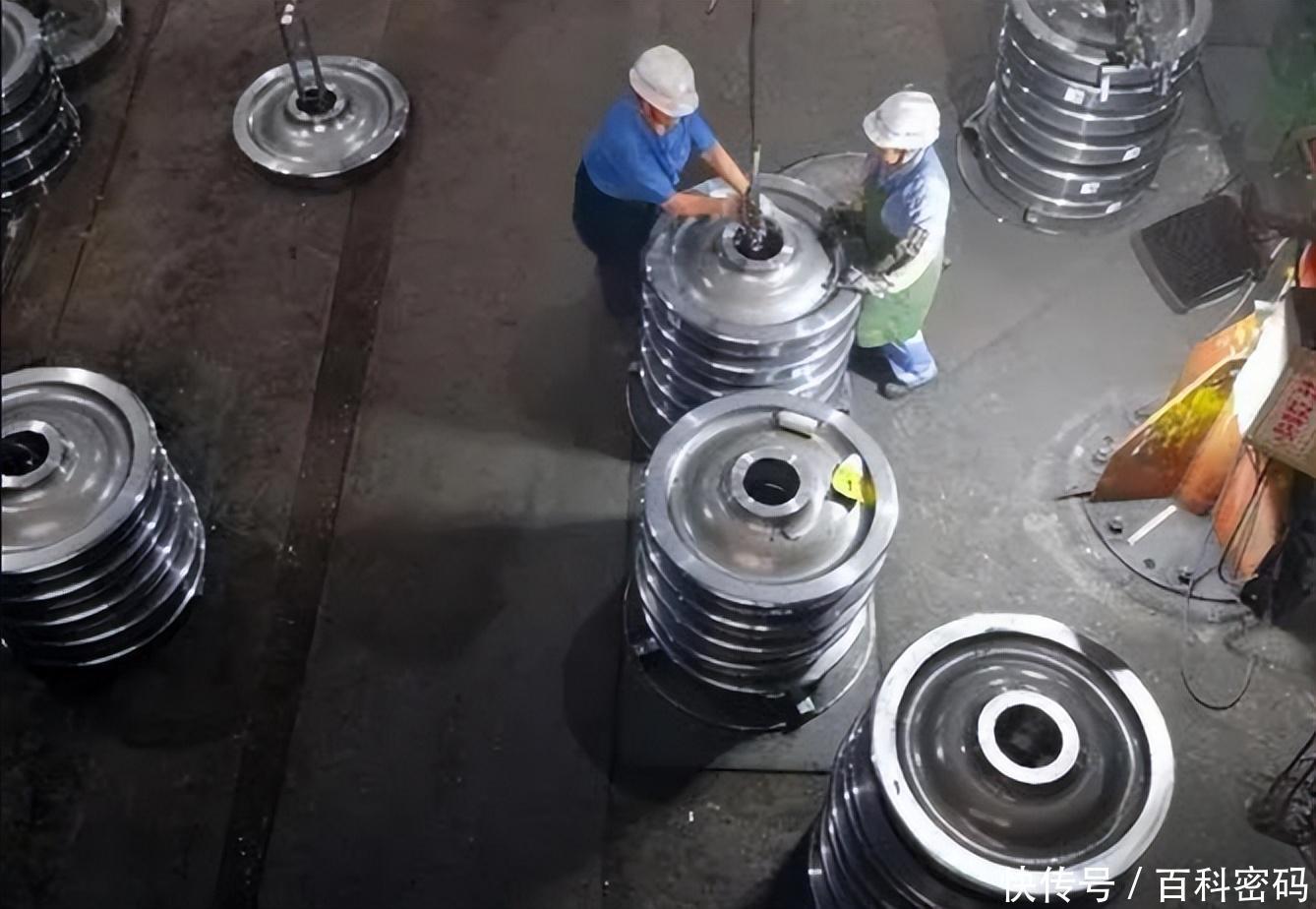
对钢材完成基本的塑形后,要进一步调整它的内部结构和成分,以达到预期的性能。热处理工艺,是指通过加热、保温和冷却的手段,使材料达到理想的组织结构和性能。在这个过程中,金属内部结构发生相变,即金属原子的排列发生改变,从而影响其性能,如硬度、韧性等。
为了让钢材达到预期的性能,加热温度和冷却速度十分关键,其最佳数值则需要通过模拟试验机进行测定。此外,在冶炼工艺中,如何利用钒元素,提升钢材的强度和硬度,也是钢材热处理的研究方向之一。
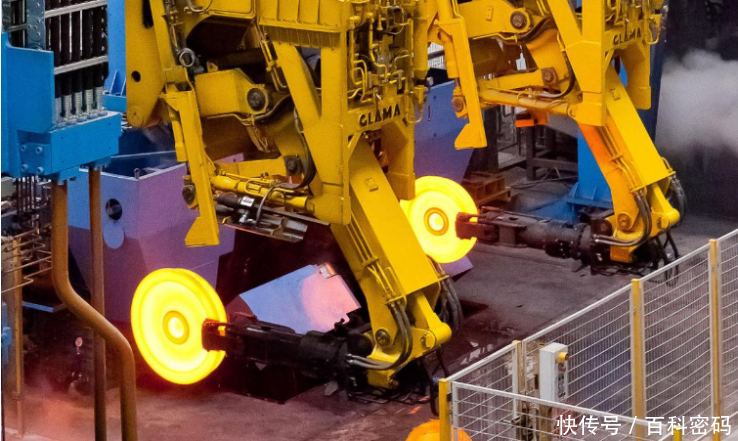
打破技术垄断的历程
纵观高铁车轮制作的全过程,我们可以看到,整个工艺流程对各个环节的参数设计要求很高,任何一个环节的细微变动,都会带来产品性能的变化。而这一点变化,很可能会在环境多变的行驶过程中,带来引发各类事故的可能,或者加速车轮的老化。
我国高铁车轮的转折点,就是目前装载于复兴号的D2型号高铁车轮,经检测,在强度、硬度性能和韧性水平上,均不低于进口车轮,甚至部分指标更具备优势。这里的“D2”,指的是这种车轮采用的是高碳高铬钢。
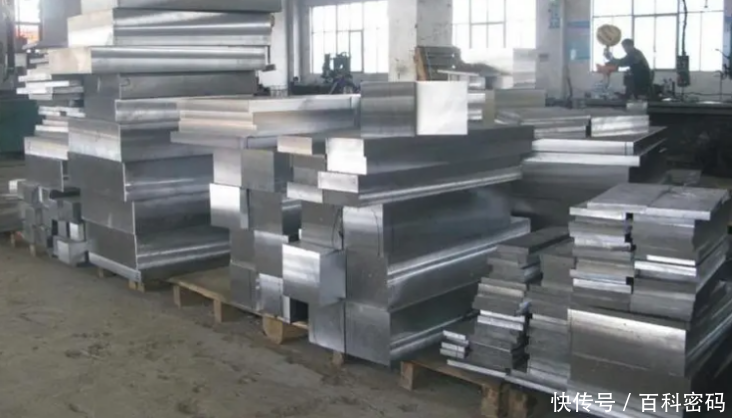
D2作为我国自主研发的高铁车轮的代表,经过不同地域、长时间、不同线路条件的严苛考验,已充分证明了自身的实力,较之进口车轮毫不逊色。如今,D2型车轮已经装用于5列350km/h的复兴号动车组上,相继在京广和京津等客运专线服役。
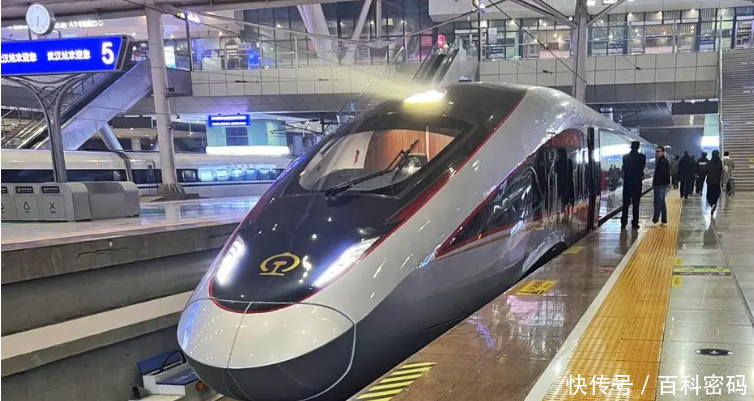
在今日的成就上,回望过去,这数十年来的技术进步,离不开科研人员的不懈努力。
2008年,为了打破四国的技术垄断,作为高铁车轮生产的中流砥柱,马钢集团启动了高铁车轮国产化项目——这就是我国自主研发车轮的开始。
马钢,全称马鞍山钢铁股份有限公司,其前身是1953年成立的马鞍山铁矿长,至今已有70多年的历史。在高铁车轮生产上,马钢贡献了不可小觑的技术力量。
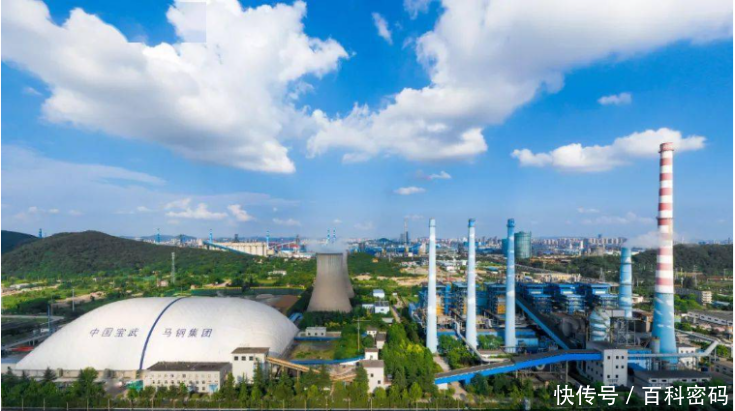
技术的进步少不了对先进技术的借鉴学习,2014年6月1日,马钢以资产收购的方式收购了法国瓦顿公司的全部资产,而这家公司是世界著名的高铁轮轴制造企业。这一举措,为我国的技术进步提供了重要支持。在对先进技术的参考和创新下,马钢研发出了碳硅板复合车轮。
同年,“动车组关键技术自主创新深化研究——时速350公里中国标准动车组轮轴设计研究”重大课题正式成立,其中以高铁车轮为研发重点。
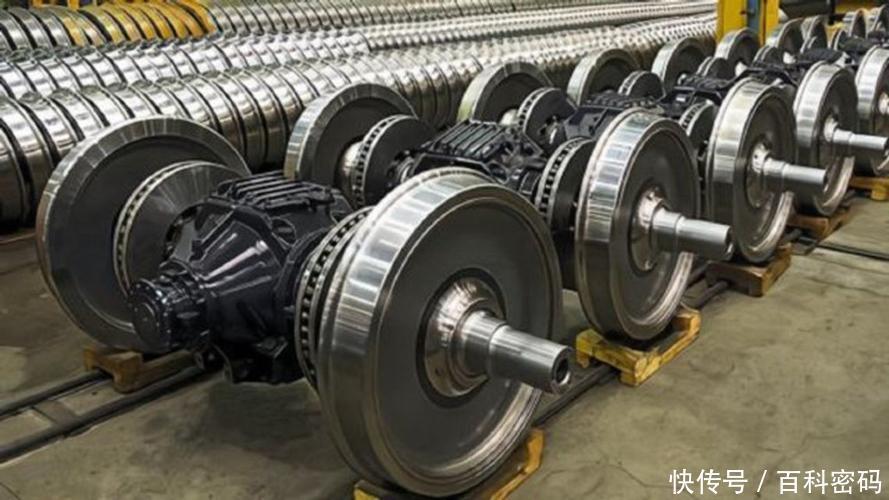
2017年年初,马钢高速动车组车轮获得了国内首张CRCC证书。这个证书以ISO9001《质量管理体系要求》为标准,而ISO9001质量管理体系是很多国家,尤其是发达国家多年的实践总结,也是迄今为止世界上最成熟的管理体系和标准。
2022年,马钢高速车轮在复兴号高速综合检测车上,实现了整车装用,这意味着我国高铁车轮已经在350公里的时速上顺利运行。而在2023年,福厦线高铁的一场装车实验中,马钢高铁车轮甚至刷新了最高记录,达到453公里的时速。
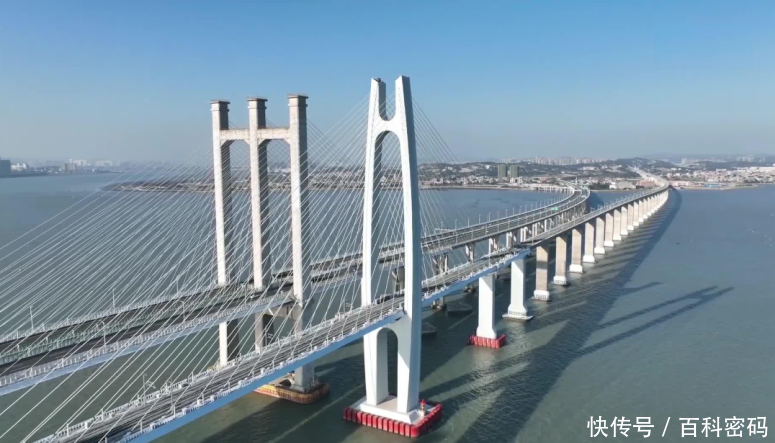
这种时速达到450公里的车轮,预计在2025年投入使用,有望成为全球最快的高速列车,大大提升了我国交通的便捷性。
车轮生产最新技术如何?
至于我国高铁车轮的最新技术具体如何,从一些文献中,我们可以窥得一二。
按照高铁车轮的生产流程,以马钢公司为例,我国在钢坯冶炼、热成型、热处理的三个工序上都有长足进步。
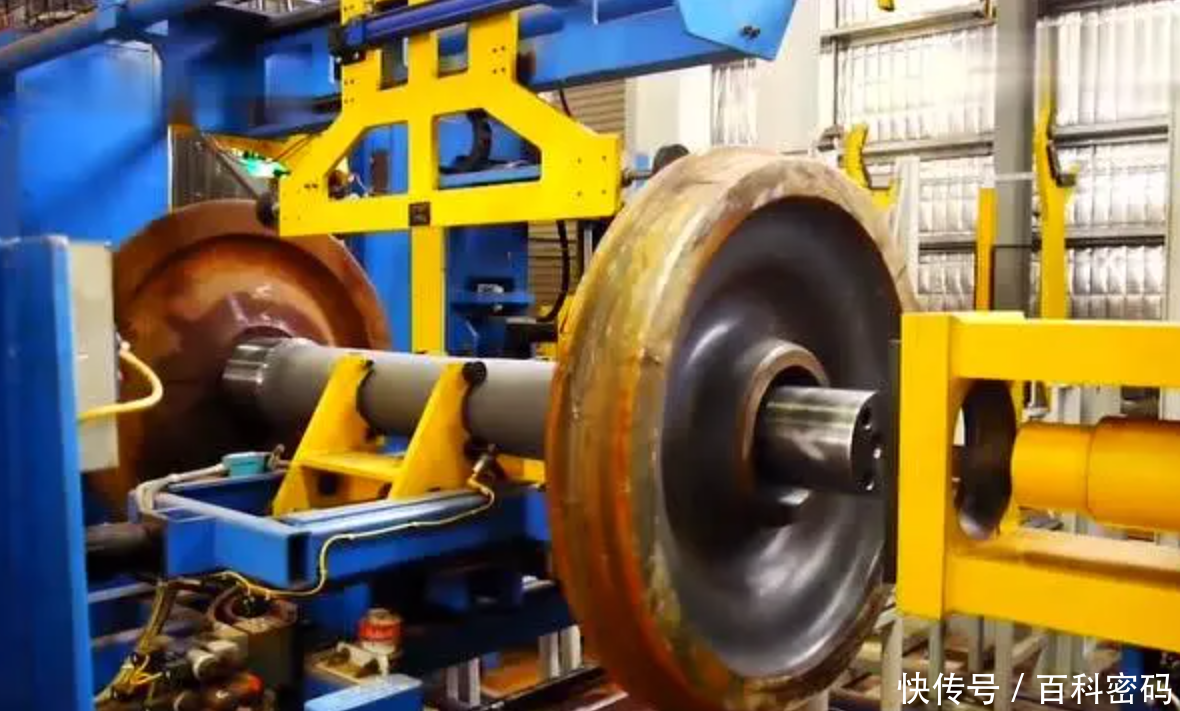
在钢坯冶炼工艺中,马钢的铸坯无氧化保护浇注技术、结晶电磁搅拌技术,都极大提升了钢材的纯净度,增强了车轮的抗疲劳性。
其中,铸坯无氧化保护浇筑技术,通过对连铸过程添加覆盖剂等操作,防止钢材的氧化,减少与空气接触的杂质。结晶电磁搅拌技术,则采用一种特殊的、由小电磁搅拌和大电磁搅拌相结合的工艺,防止在钢材逐渐冷却的过程中,因碳元素凝固不均匀发生的碳偏析现象,使钢材性能更稳定。
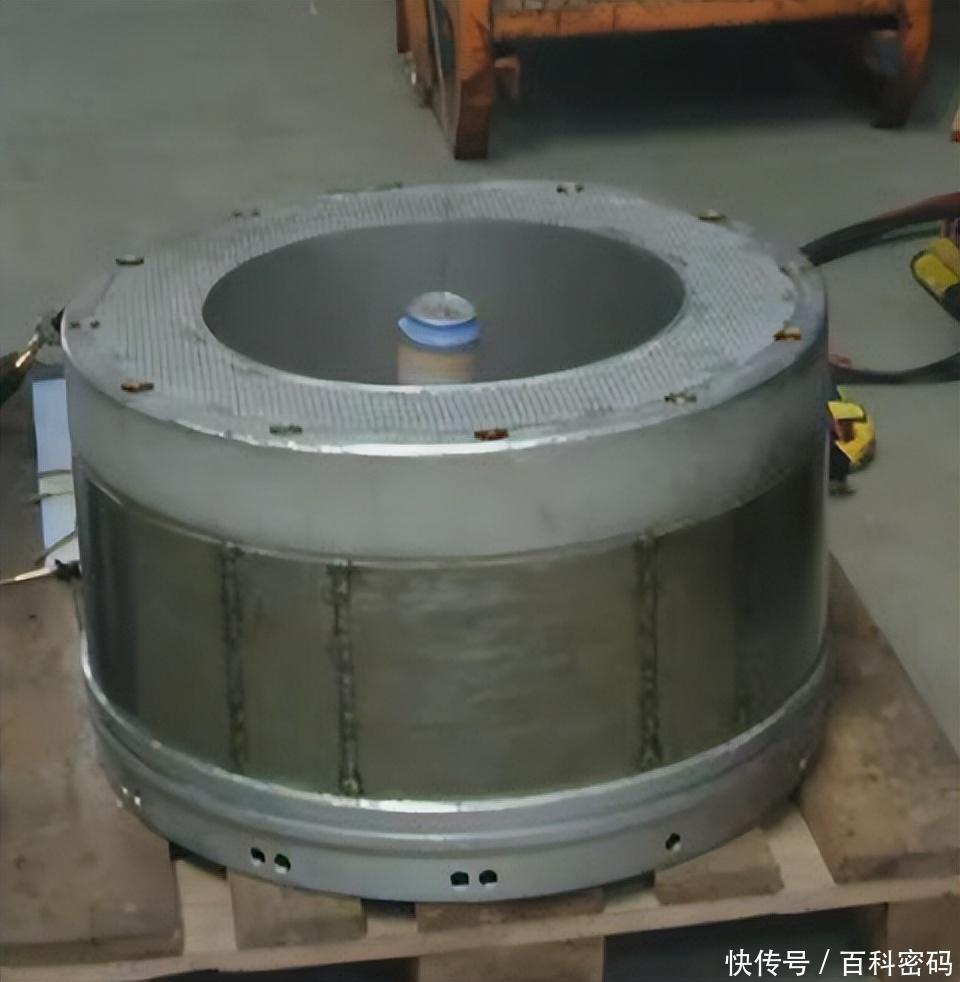
在热成型工艺中,为了实时对加热温度进行分析,以便调整工艺的参数设计,需要对温度进行准确的测量。
马钢通过数值模拟的方法,对圆坯加热过程进行分析,得到了温度分布的模拟值,然后利用DataPaq在线测温系统,沿钢坯中轴线植入测温元件,对车轮圆坯加热过程温度进行了测量,得出测量值与模拟结果吻合的结果。这一温度测量的方法,通过控制加热温度,间接使得车轮中成分的分布更为均匀。
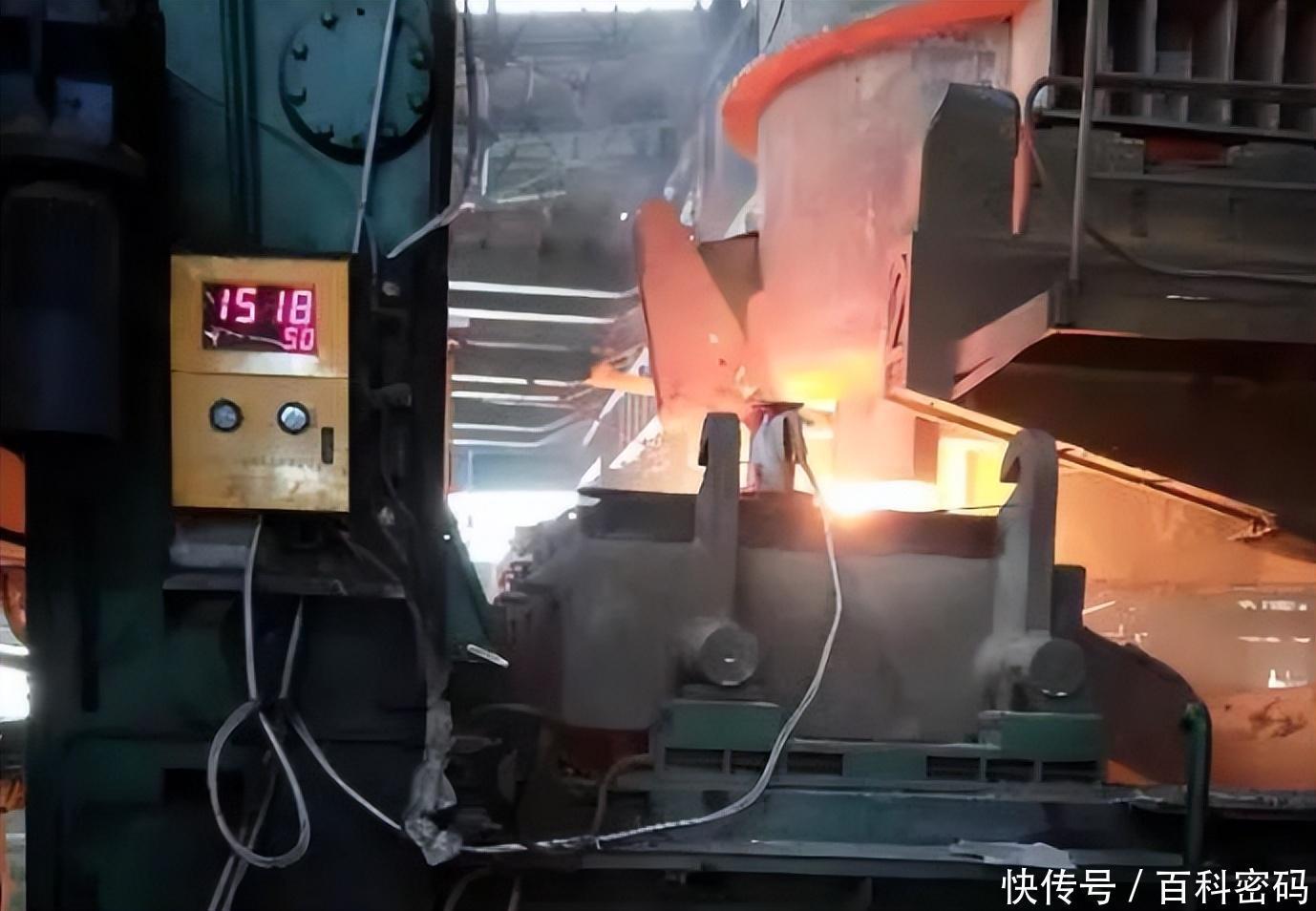
在热处理工艺中,为了确定加热温度和冷却速度的最佳数值,更好地发挥钒元素对车轮的强化和成分细化作用,则需要通过模拟试验机测定。
马钢利用Formastor热模拟试验机对各种常见材料进行测定,同时通过金相显微镜观察材料的组织结构,观察加热温度、冷却速度与硬度的相关性,并对成品进行硬度测试。这个测验确定了车轮热处理的各项最佳参数,并辨析了材料之间硬度随冷却速度变化的不同,进一步为提升车轮性能提供了参考。
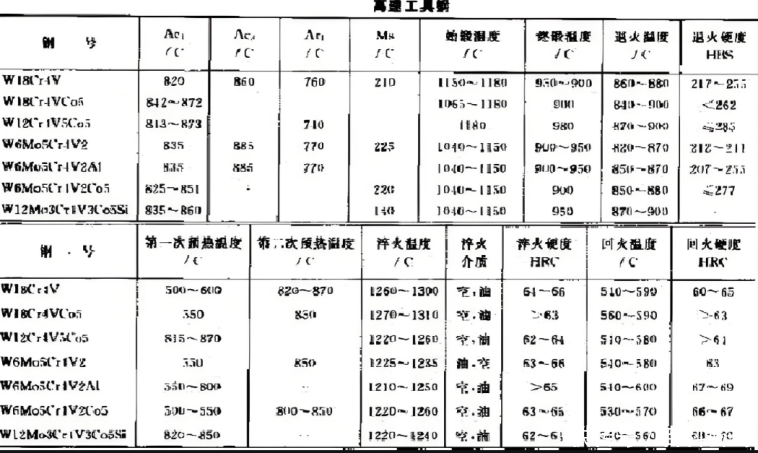
在这些先进生产技术的基础上,各国了解到我国的技术优势,也开始主动与我国高铁车轮制造企业进行合作。其中,德国铁路公司与马钢签订了供货合同,并连续订购了约160件车轮,并成功投入运行。此后,韩国、印度等国家,也陆续从我国进口高铁车轮。
我国生产的高铁车轮,不但能在东北零下30℃的冬季正常运行,同样也能在超过40℃的南方地区保持性能稳定,且在部分沿海地区的铁路线上,即使受到海风和盐雾的长期侵蚀,依然有优秀的安全可靠性。我国自主生产的高铁车轮如此优秀,难怪以前的四大强国也要从我国进口,填补车轮供应的缺口。
友情提示
本站部分转载文章,皆来自互联网,仅供参考及分享,并不用于任何商业用途;版权归原作者所有,如涉及作品内容、版权和其他问题,请与本网联系,我们将在第一时间删除内容!
联系邮箱:1042463605@qq.com